What is CAN Bus and How Does It Work?
Introduction to CAN Bus
The Controller Area Network (CAN) Bus is a robust communication protocol widely used in automotive and industrial systems. Developed by Bosch in the 1980s, it enables microcontrollers and devices to communicate with each other without a host computer. Today, CAN Bus is a cornerstone of vehicle electronics, powering everything from engine control units to fleet management tablets and taxi tablets.
This article dives into what CAN Bus is, how it operates, its applications, and why it’s critical for modern vehicles and industrial automation. Whether you’re a fleet manager, automotive technician, or tech enthusiast, understanding CAN Bus will give you insight into the backbone of connected systems.
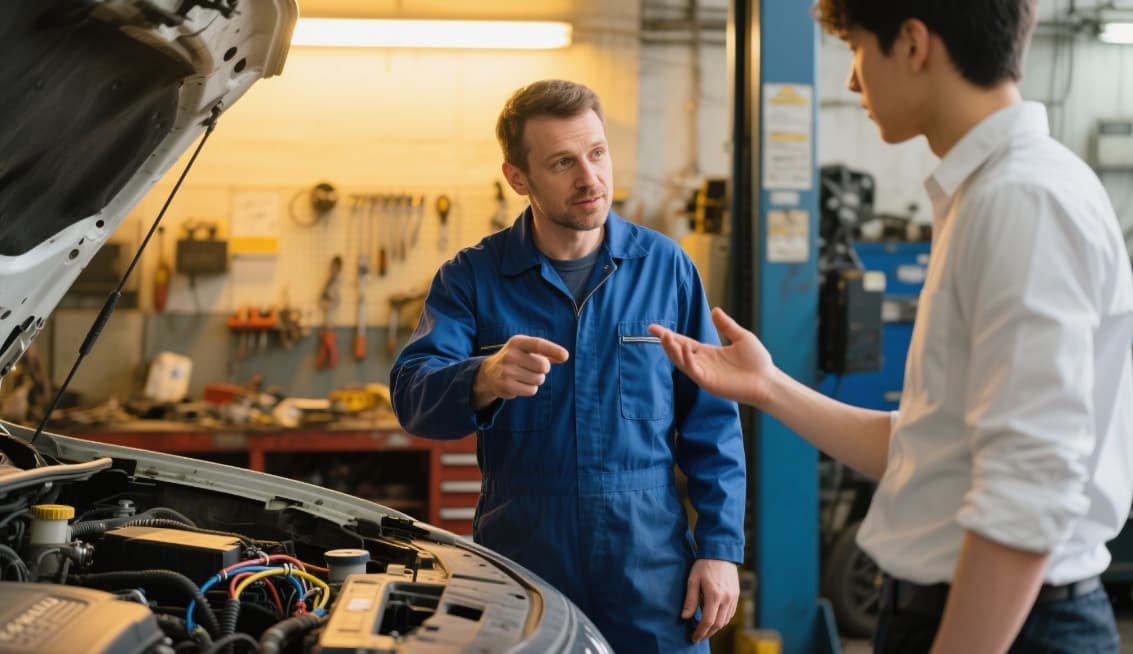
What is CAN Bus?
CAN Bus is a serial communication protocol designed for real-time, reliable data exchange in harsh environments, such as vehicles and industrial machinery. Unlike traditional point-to-point wiring, CAN Bus uses a multi-master, message-based system, allowing multiple devices to share a single communication line. This reduces wiring complexity, weight, and cost, making it ideal for automotive applications.
The protocol is standardized under ISO 11898, ensuring compatibility across devices and manufacturers. Its key features include:
- Error Detection: Built-in mechanisms like CRC (Cyclic Redundancy Check) ensure data integrity.
- Fault Tolerance: CAN Bus can operate even if one node fails, maintaining system reliability.
- Scalability: It supports hundreds of nodes, making it suitable for complex systems.
- Real-Time Communication: Low-latency data transfer supports critical applications like braking systems.
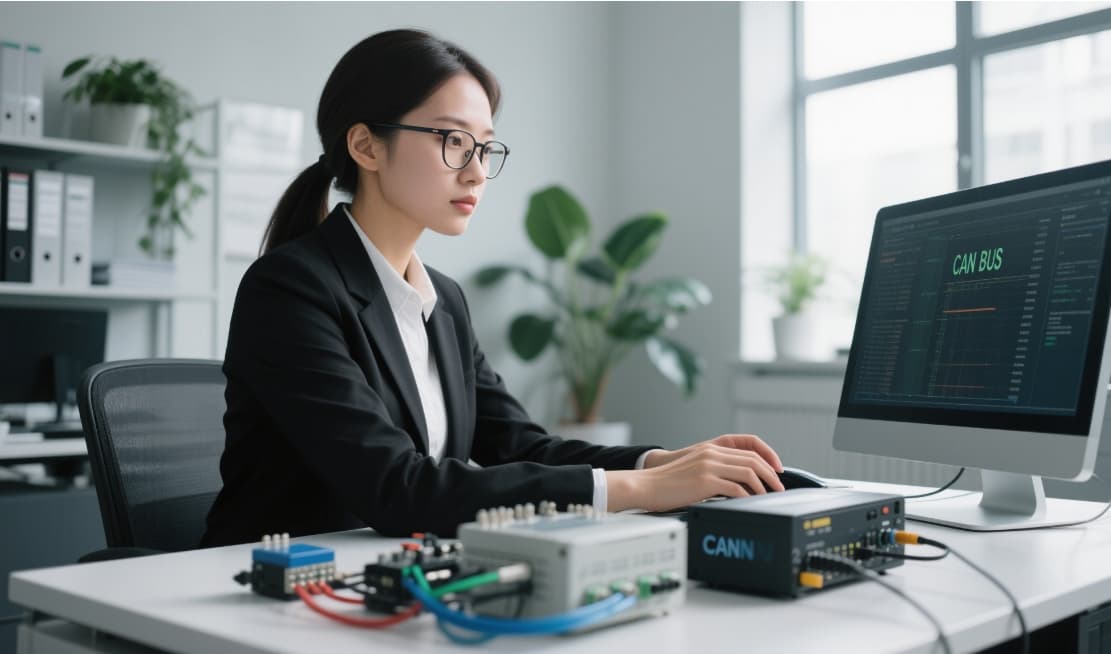
How Does CAN Bus Work?
CAN Bus operates on a two-wire differential signaling system, typically referred to as CAN_H (high) and CAN_L (low). These wires carry signals that allow devices, or “nodes,” to communicate. Each node can send or receive messages, but only one node transmits at a time to avoid collisions.
Key Components of CAN Bus
- Nodes: Devices like sensors, actuators, or control units connected to the CAN Bus.
- CAN Controller: A microcontroller or chip that manages message transmission and reception.
- CAN Transceiver: Converts digital signals into differential signals for the bus and vice versa.
- Bus Lines: The physical wires (CAN_H and CAN_L) that connect all nodes.
Message Transmission
CAN Bus uses a message-based protocol, where data is sent in packets called frames. Each frame contains:
- Identifier: A unique ID that determines the message’s priority and content.
- Data Field: Up to 8 bytes of actual data (e.g., sensor readings).
- Control Bits: Information about the frame’s length and type.
- CRC: Ensures the message is error-free.
When a node transmits a message, all other nodes receive it but only process relevant messages based on the identifier. If multiple nodes try to send messages simultaneously, the one with the highest-priority identifier wins through a process called arbitration.
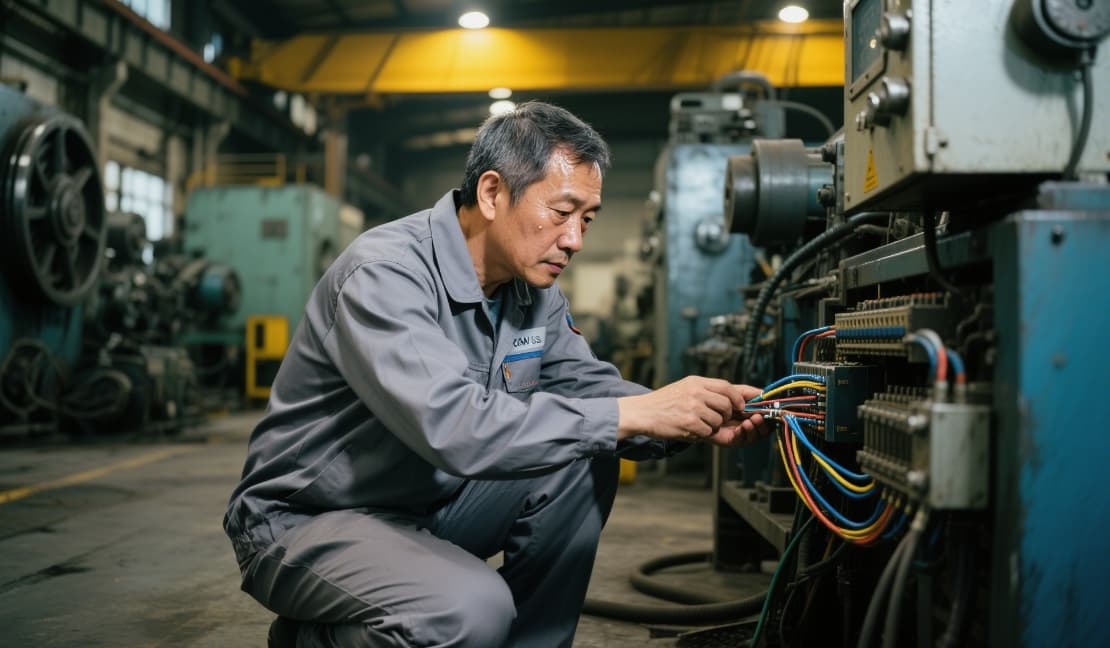
Arbitration and Priority
Arbitration is a key feature of CAN Bus. It ensures collision-free communication by allowing nodes to compete for bus access. The node with the lowest identifier value (highest priority) continues transmitting, while others wait. This non-destructive arbitration ensures critical messages, like those from an anti-lock braking system, are prioritized over less urgent ones, such as infotainment data.
Applications of CAN Bus
CAN Bus is ubiquitous in industries requiring reliable, real-time communication. Below are some key applications:
Automotive Systems
In vehicles, CAN Bus connects critical systems like:
- Engine Control Unit (ECU): Manages fuel injection, ignition timing, and emissions.
- Transmission Control: Ensures smooth gear shifts.
- Anti-Lock Braking System (ABS): Coordinates braking for safety.
- Infotainment Systems: Integrates navigation, audio, and connectivity.
It’s also integral to vehicle diagnostics, enabling tools like OBD-II scanners to read error codes and monitor performance.
Fleet Management Tablets
Fleet management tablets rely on CAN Bus to collect real-time vehicle data, such as fuel consumption, speed, and engine health. This data helps fleet managers optimize routes, reduce costs, and ensure compliance with regulations. For example, a tablet connected to the CAN Bus can display diagnostic trouble codes (DTCs) or track driver behavior, improving safety and efficiency.
Taxi Tablets
In the taxi industry, taxi tablets use CAN Bus to integrate payment systems, GPS navigation, and vehicle diagnostics. These tablets communicate with the vehicle’s CAN network to monitor mileage, fuel levels, and maintenance needs, ensuring a seamless experience for drivers and passengers.
Industrial Automation
Beyond automotive, CAN Bus is used in factory automation, medical equipment, and aerospace. Its ability to handle noisy environments and support multiple devices makes it ideal for controlling robotic arms, conveyor systems, and more.
Advantages of CAN Bus
CAN Bus offers several benefits that make it a preferred choice for communication in complex systems:
- Cost-Effective: Reduces wiring and hardware costs by using a single bus.
- Reliable: Robust error detection and fault tolerance ensure consistent performance.
- Flexible: Easily integrates new nodes without rewiring.
- Efficient: Prioritizes critical messages for real-time applications.
Challenges and Limitations
While CAN Bus is highly effective, it has some limitations:
- Limited Bandwidth: The maximum data rate (1 Mbps for standard CAN) may not suffice for data-intensive applications like autonomous driving.
- Data Length: The 8-byte data field limits the amount of information per frame.
- Complexity: Implementing and troubleshooting CAN Bus requires specialized knowledge.
Modern variants like CAN FD (Flexible Data Rate) address some of these issues by offering higher data rates and larger payloads, making them suitable for next-generation vehicles and IoT devices.
Frequently Asked Questions (FAQ)
1. What does CAN Bus stand for?
CAN Bus stands for Controller Area Network Bus. It’s a communication protocol that allows multiple devices to exchange data over a single bus line.
2. How is CAN Bus used in fleet management?
CAN Bus provides real-time vehicle data to fleet management tablets, enabling managers to monitor fuel efficiency, driver behavior, and maintenance needs.
3. Can CAN Bus be hacked?
While CAN Bus is secure for its intended purposes, vulnerabilities exist if physical access is gained. Modern vehicles use encryption and gateways to mitigate risks.
4. What’s the difference between CAN and CAN FD?
CAN FD (Flexible Data Rate) is an advanced version of CAN, offering higher data rates and larger payloads, making it suitable for modern applications like autonomous vehicles.
5. How does a taxi tablet use CAN Bus?
A taxi tablet connects to the CAN Bus to access vehicle data like mileage and fuel levels, integrating it with navigation and payment systems.
Conclusion
The CAN Bus is a game-changer in automotive and industrial communication, offering reliability, efficiency, and scalability. From powering vehicle diagnostics to enabling fleet management tablets and taxi tablets, its impact is undeniable. As technology evolves, variants16, advancements like CAN FD ensure CAN Bus remains relevant for future innovations.
Understanding CAN Bus empowers fleet managers, technicians, and enthusiasts to leverage its capabilities for smarter, safer, and more efficient systems. Whether you’re optimizing a taxi service or managing a fleet, CAN Bus is the silent force driving connectivity.